An elastomer is essentially an elastic polymer. Types of elastomers include silicone, synthetic rubber, EDPM, natural rubber, SBR, isoprene rubber, and more. Elastomers are perfect for molding because they are incredibly flexible and provide high performance once molded. Parts made out of molded elastomer are used for a variety of applications and offer many benefits. Continue reading to learn more about elastomer molding.
Types of Elastomer Molding
To be transformed into a useful product, elastomers can be molded using a few different methods. The outcome of these methods vary. Companies may choose a specific molding process based on cost, speed, precision, and purpose. Each method requires specific materials and equipment. Here are the four most frequently used approaches for molding elastomer:
Injection molding: This is the most common way that elastomers are molded because it is quick and precise. The elastomer is first melted down so that it can be put into the injection unit. Then, the melted elastomer is injected into the mold. Once injected, it is either vulcanized or cooled so that it forms the shape of the mold, creating an elastomer molded part.
Compression molding: This molding process is the next most common. To make the elastomer fit into the shape, the mold is preheated. Then, solid rubber is put into the heated mold where it begins to soften. The machine compresses the elastomer so that it conforms to the mold. After this, the rubber is cured through cooling or vulcanization.
Transfer molding: Similar to the injection molding process, transfer molding heats the elastomer and not the mold. The liquid elastomer remains in a pot until the molding process begins. A plunger pushes the elastomer into the closed mold where it forms the shape after being cooled or vulcanized. Transfer molding is often used for sealing electronic parts.
Cast molding: This molding process includes using a liquid elastomer. It is poured into a hot mold and then moved to an oven to cure. The mold is only removed when the material has completely hardened. Most cast molded rubber has to be cured two times.
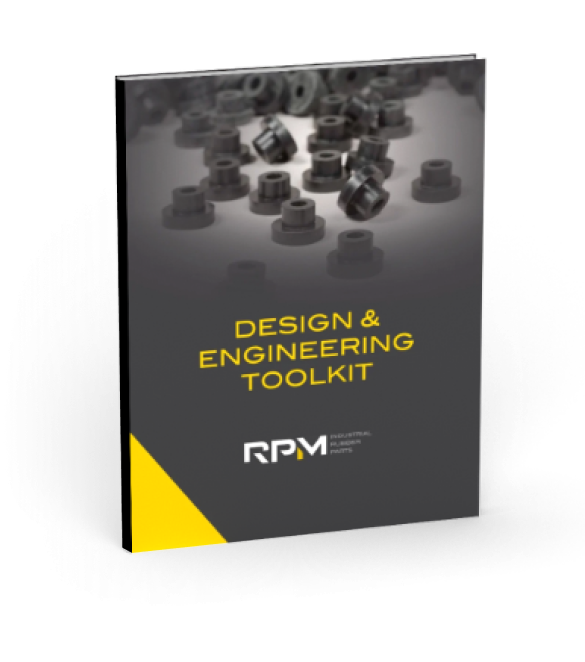
Do you really know everything about designing with rubber parts?
Get a free and valuable resource for finding or custom designing the exact part you need.
How Molded Elastomer is Used
There are many different applications for molded elastomers. Because this category of materials can range from a polymer to liquid silicone rubber materials, there is a wide range of uses. Here are some of the most common uses of molded elastomers:
- Automotive: Door Panel bumpers, gaskets, weather stripping, radiator seals, exhaust hangers
- Aerospace: Gaskets, weather stripping, engine mounts, electrical insulation.
- Medical: Electrical insulation, surgical devices, grommets, grips, connector.
- Construction: Vibration reducer, anti-slip, window seals, equipment parts, bumpers.
- Food and beverage: Silicone mats, carts, seals.
- Agriculture: Tubing, vibration control, equipment parts, weather stripping, hydraulic seas.
Because elastomers are so versatile, the above applications only touch the surface of how they can be used. The right manufacturing process and curing process can create molded parts that withstand extreme temperatures, chemicals and vibration. They also have exceptional tensile strength. Just about every industry requires elastomeric material in manufacturing or production machines and equipment
Benefits of Elastomer Molding
There are advantages for every type of elastomer molding process. This is why so many manufacturers, in all industries, choose elastomer molding over other rubber processes. Here are some of the benefits of elastomer molding:
Customization capabilities: Because elastomer molding is already so versatile, it is the perfect method to produce custom molded rubber parts. Manufacturers are better able to produce these custom parts because elastomer molding makes it easier. and durability.
High production speed and volume: When manufacturers choose processes like injection or compression molding, they can produce parts at a high speed and volume. These methods are optimal for big batch parts.
Versatility: Just about every molding method can be used with a variety of different elastomers. For example, many manufacturers use silicone for injection molding and synthetic rubber for compression molding.
Precision and quality: With elastomer molding, manufacturers will find that products come out with minimal or no imperfections. Molded products align with high-quality standards. Some methods offer more precision than others.
Quality Custom Molded Rubber Parts
With elastomer molding methods, companies can produce quality, specially made custom rubber parts. One of these companies is RPM: Industrial Rubber Parts. Our team is ready to help our customers find the parts that they need. If we don’t have the part that you need and we can’t find it, then we’ll make it.
RPM works one-on-one with customers through all aspects of elastomer molded parts. Our in-house engineers will create drawings of your design. Then, they will create a prototype to send to you. Once you are satisfied with the prototype, we will manufacture and ship the order.
RPM also offers a variety of standard parts such as vibration control, bumpers, grommets, mounts, bushing, bearings, and more. Our team believes in providing only the highest quality rubber parts made with advanced molding technology. If you are looking for an excellent rubber part and custom rubber part manufacturer, we can help.
To get in touch with our team at RPM Industrial Rubber Parts, give us a call at (888) 842-5668 or contact us online.
Related Resource
The Engineer’s 7-minute Guide to Rubber Molded Parts
Our free resource is a quick-reference guide to help you determine if exploring a rubber part is right for your application.