In the world of industrial machinery and equipment, minimizing vibration and enhancing stability are paramount for ensuring longevity and optimal performance.
Enter the unsung hero of vibration isolation and shock absorption: the rubber sandwich mount.
But what exactly is a rubber sandwich mount, and why is it considered an essential component in a wide array of applications?
This innovative solution, often overlooked, plays a critical role in safeguarding machinery by mitigating the effects of mechanical vibrations and shocks.
In this guide, we delve into the anatomy of rubber sandwich mounts, exploring their design, functionality, and the myriad of benefits they offer. Whether you’re an engineer seeking to enhance machine performance or simply curious about the mechanics behind these vital components, you’re in the right place to uncover the significance of rubber sandwich mounts in the industrial world.
Unlocking the Advantages of Rubber Sandwich Mounts
Rubber sandwich mounts stand out as a cornerstone in the realm of vibration isolation and shock absorption, offering a suite of advantages that underscore their importance across various industries. Here’s a closer look at the unparalleled benefits these robust components deliver:
Exceptional Load Capacity: Designed to withstand the rigors of heavy-duty applications, rubber sandwich mounts boast an impressive load-bearing capacity. Capable of supporting up to 7,000 lbs in compression static loads, they are engineered to meet the demands of even the most challenging environments.
Simplified Installation Process: The streamlined design of rubber sandwich mounts not only contributes to their effectiveness but also ensures ease of installation. This user-friendly attribute allows for quick and efficient setup, saving valuable time and effort.
Zero Maintenance Hassle: Crafted from high-quality rubber, these mounts are inherently maintenance-free. The durability of rubber eliminates the need for regular upkeep, making rubber sandwich mounts a cost-effective solution for long-term use.
Enhanced Compressive Strength: The ability to absorb and manage energy through compression is a hallmark of rubber sandwich mounts. This feature translates into superior vibration damping and shock reduction, ensuring the protection and stability of machinery and equipment.
Superior Durability through Metal-to-Rubber Bonding: The construction of rubber sandwich mounts involves a metal-to-rubber bonding process that guarantees exceptional durability. This strong bond ensures that the mounts maintain their integrity and performance over time, even under continuous stress and movement.
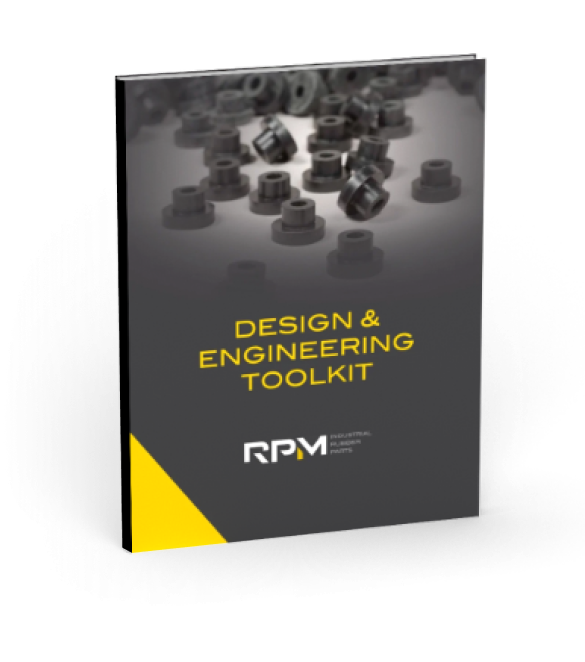
Do you really know everything about designing with rubber parts?
Get a free and valuable resource for finding or custom designing the exact part you need.
Sandwich Mount Design
There are a few designs for sandwich mounts that will best suit specific applications. Most often, a sandwich mount consists of a rubber cylinder with a metal plate and stud on both ends. Some sandwich mounts may have one metal plate, or none at all, while some will have one stud or none at all. Again, it depends on the specific mount and its intended use.
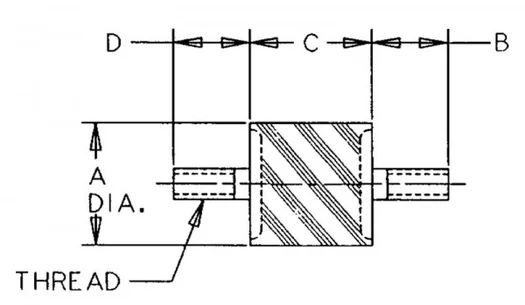
Take a look at the different kinds of sandwich mounts:
Bobbin sandwich mounts
Large shear mounts
Square pad mounts
LORD Flex-Bolt™ Sandwich Mounts
Some sandwich mounts look completely different, although the concept stays the same. For example, large shear mounts have two square metal plates with a cylindrical rubber piece in the middle. The metal plates do not have any studs. Instead, they have multiple holes for the studs to go once installed.
Sandwich Mount Function
The core purpose of a rubber sandwich mount lies in its ability to mitigate vibration and shock, a critical factor in maintaining the integrity and performance of machinery. This is achieved through its innovative compressive design paired with vibration-damping materials.
Consider a scenario where a piece of machinery operates with unchecked vibration. Positioned on a shop floor or within a warehouse, this vibration can lead to potential harm not only to the machinery itself but also to the products being handled and the operators overseeing the process.
The introduction of a rubber sandwich mount into this equation changes the dynamics entirely. By securely attaching a specially designed rubber element between the machine and the floor, the vibrations are significantly reduced, if not entirely eliminated.
Rubber sandwich mounts function by effectively compressing between two surfaces, thereby absorbing and isolating the vibrations within the rubber material itself. This not only protects the machinery and reduces wear and tear but also safeguards the workplace environment from the adverse effects of excessive vibration.
Furthermore, these mounts serve a dual purpose by acting as buffers within spring mounts, providing an additional layer of vibration control. They are particularly beneficial in applications involving sensitive equipment, where even minimal vibration can lead to significant disruptions or damage.
The indispensable role of rubber sandwich mounts in enhancing the operational efficiency and longevity of machinery cannot be overstated, underscoring their value in a wide range of industrial settings.
Sandwich Mount Materials
The construction of rubber sandwich mounts involves a careful selection of materials, each chosen for its unique properties and contribution to the mount’s overall performance. At the heart of these mounts are two primary components: the metal elements and the rubber polymers, each playing a pivotal role in the functionality and durability of the mount.
Metal Components: The Backbone of Durability: The structural integrity of sandwich mounts is largely attributed to their metal components, typically comprising studs and plates made from steel, aluminum, or stainless steel. These metals are selected for their exceptional strength and durability, offering robust support at a cost-effective price point. Their resilience ensures that sandwich mounts can withstand the rigors of industrial use, providing a reliable foundation for the vibration damping capabilities of the rubber polymers.
Rubber Polymers: The Essence of Vibration Damping: Rubber polymers are at the core of a sandwich mount’s ability to absorb and dampen vibration. The choice of rubber is critical, as each polymer variant brings its own set of characteristics to the table:
- Natural Rubber: Predominantly used for its superior vibration reduction and fatigue resistance, natural rubber is the go-to choice for many applications. Its main limitation, however, lies in its susceptibility to extreme temperature variations, which can affect its performance.
- Silicone: Not all silicone is created equal. High-quality silicone, such as that developed by specialized manufacturers like LORD, offers enhanced vibration and temperature resistance, making it a premium choice for environments where both factors are a concern. Despite its lower tear resistance in standard forms, this specialized silicone stands out for its performance in demanding conditions.
- Neoprene: Valued for its high tensile strength and resistance to abrasion, neoprene is another popular choice for sandwich mounts. Its resilience to oils and chemicals, although not impervious, allows it to be used in environments where such exposures are possible.
While these materials represent the most commonly used polymers in the construction of sandwich mounts, the selection is by no means limited to these options. The ultimate choice of material depends on the specific requirements of the application, including factors such as load-bearing capacity, environmental conditions, and the nature of the vibrations to be dampened.
Need Help with Your Sandwich Mount?
The materials used in rubber sandwich mounts—ranging from robust metals to versatile rubber polymers—play a crucial role in their ability to provide effective vibration isolation and shock absorption. The careful selection of these materials ensures that each mount is not only strong and durable but also precisely tailored to meet the demands of its intended use. Contact us for assistance with your sandwich mount material selection.
To get in touch with our team at RPM Industrial Rubber Parts, give us a call at (888) 842-5668 or contact us online.
Related Resource
The Engineer’s 7-minute Guide to Rubber Molded Parts
Our free resource is a quick-reference guide to help you determine if exploring a rubber part is right for your application.