Markets Served
Medical Industry
The medical industry is one of the top users of rubber parts. From CT scanners to dialysis machines, rubber parts ensure critical equipment functions the way it should. Medical equipment is designed and manufactured following strict standards. These standards ensure that equipment is durable and reliable. Lifesaving equipment isn’t much help if it breaks at random. More +
Rubber Parts & Medical Equipment Applications
RPM offers advanced rubber molding solutions tailored to meet precise specifications and industry standards. With expertise in compression, transfer, and injection molding, we deliver high-quality, durable rubber components designed for diverse applications.
Application | Common Parts | Common Processes |
---|---|---|
Infusion & Oxygen Pumps | Rubber seals, vibration mounts, grommets, and bushings used to reduce noise and protect bolting machinery components from wear. | Compression molding for durability and high resistance to tearing, injection molding for complex shapes and precise tolerances. |
Dialysis Machines | Door seals, rubberized flooring, suspension bushings, and noise-dampening pads to ensure safety and comfort for operators. | Transfer molding to create durable, shock-absorbing parts, extrusion for flexible seals and tubing. |
Laboratory Equipment | Drill head seals, anti-vibration pads, and rubber bushings designed to protect drilling components from impact and abrasion. | Precision extrusion for high-quality seals, vulcanization for enhanced material properties like heat and wear resistance. |
IV & Catheter Tubing | Weather-resistant seals, vibration dampeners, rubber grommets, and protective boots for wiring and moving parts. | Compression molding for long-lasting durability, injection molding for custom shapes and parts, die-cutting for precise component production. |
Sensors & Electronic Systems | Rubber buffers, hydraulic seals, wear pads, and anti-slip mats to enhance safety and maintain equipment longevity. | Injection molding for intricate parts, precision die-cutting for custom shapes, and vulcanization for improved mechanical properties. |
CT Scanners | Shock-absorbing rubber pads, high-impact seals, dust boots, and vibration control mounts used to withstand high-pressure environments. | Compression molding for robust, wear-resistant parts, transfer molding for strong, flexible components, vulcanization for enhanced impact and abrasion resistance. |
X-ray Machines | Seals for high-pressure hoses, rubber diaphragms, gaskets for spray nozzles, and flexible tubing to withstand chemical exposure. | Extrusion for long, flexible seals and tubing, compression molding for durable gaskets and seals, vulcanization to improve chemical and temperature resistance. |
MRI Machines | Rubberized cable protectors, shock-absorbing mounts, impact-resistant seals, and gaskets for secure, safe handling of explosive materials. | Injection molding for high-precision parts, compression molding for impact resistance, vulcanization for enhancing durability and safety properties under high-stress conditions. |
Use our interactive infographic to find rubber parts for your Medical application:
Medical applications contain many different parts. Our custom rubber molding blog can tell you everything you need to know about the different types of rubber we use at RPM. Standard rubber parts don’t always cut it when it comes to new technology. Fortunately, RPM has a solution. Our custom molded rubber parts are perfect for out-of-the-box applications such as automated precision machines or AI devices.
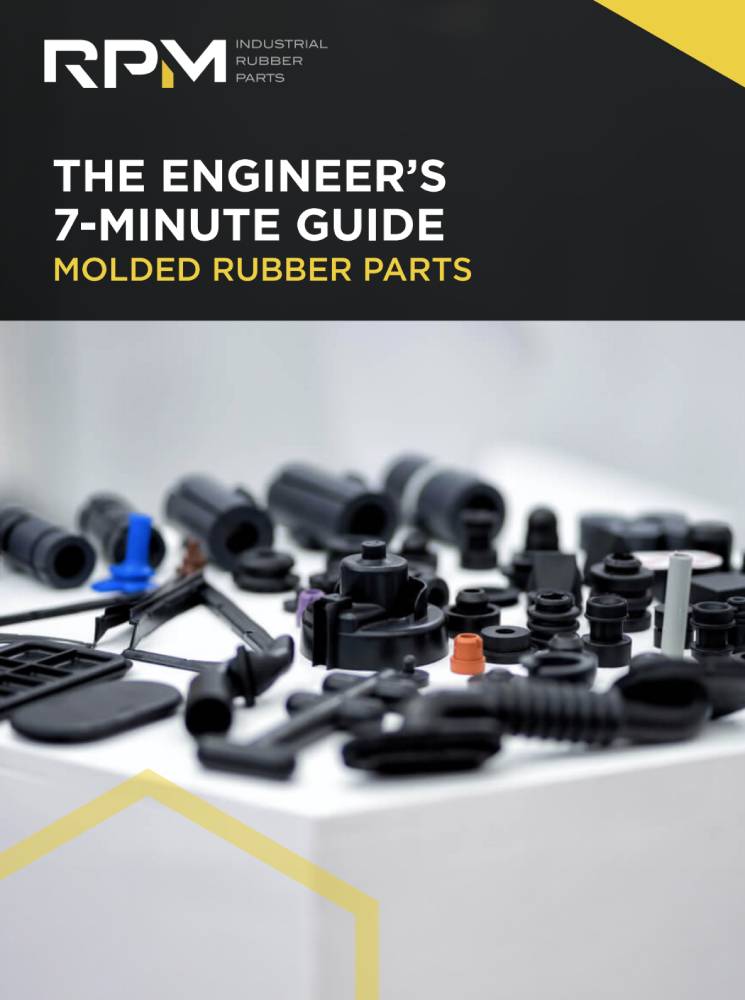
The Engineer’s 7-minute Guide to Rubber Molded Parts
Our free resource is a quick-reference guide to help you determine if exploring a rubber part is right for your application.
Challenges
Medical laboratories and patient treatment equipment is sensitive and often requires complex solutions. Typically, when manufacturing medical equipment, materials need to be medical grade. Navigating the landscape of these strict standards poses unique challenges:
Medical Grade Rubber
According to Medical Design Briefs, silicone and EPDM are considered medical grade materials because they are more likely to be approved by regulatory bodies. These materials are commonly used for medical applications because they are less likely to break down or crack after long-term use. Additionally, EPDM and silicone are fairly resistant to ozone exposure. Because some medical equipment has to be stored for long periods of time, it’s important that they don’t degrade over time.
Biocompatibility
The Food and Drug Administration is in charge of determining the biocompatibility of different materials for medical equipment. If the FDA determines a rubber as being biocompatible, it’ll be certified as an ISO 10993 rubber. A second regulatory body is the United States Pharmacopeia (USP). The USP rates materials using classes of biocompatibility. If a material passes all biocompatibility assessments, it will be certified as a USP Class VI material, which is the highest USP class.
Minimizing Vibrations
Minimizing vibration in laboratory areas is key to providing accurate lab results. Even slight vibration can skew results and damage specimens. Rubber isolates the equipment from vibration. Many patient treatment machines give off natural noise and vibration. Isolating with rubber parts ensures that these devices and tools can withstand volatile conditions.
Trends
The medical technology industry is one of the fastest growing industries in the world. In fact, according to Fortune Business Insights, in 2021, the medical technology industry was worth $488.98 billion. This number is only expected to grow.
Rubber parts don’t become obsolete as equipment becomes more lightweight, technologically oriented, and efficient. Instead, the role of the rubber part changes. Take a look at how rubber parts are utilized in two different medical technology trends.
Medical Artificial Intelligence Devices
Artificial intelligence is being utilized in all kinds of industries. AI machines can take on some of the repetitive tasks that take up the time of healthcare professionals. Artificial intelligence machines utilize quantitative data to inform their actions. In healthcare, AI is used in imaging software and wearable sensors. Sensors and other similar technology can easily break when exposed to heavy vibrations, sounds, and other harsh conditions. Small rubber mounts can be utilized to protect important sensors, chips, and software from becoming damaged by external issues.
Automated Precision Machines
Another technology that is taking the medical world by storm is automated precision machines. These machines can complete tasks as simple as filling prescription bottles to performing minor surgeries. Because the machines are focused on completing very specific tasks, they utilize sensitive equipment that keeps them functioning the right way. Similar to the way that rubber protects sensors, rubber can also protect these machines. The technology is too critical and too expensive to leave unprotected from vibration and noise.
Frequently Asked Questions

Find quick answers to your questions here or contact us directly for any additional inquiries.
What are the benefits of rubber compression molding?
Compression molding offers several advantages, including high production rates, excellent dimensional stability, and the ability to produce complex shapes with intricate details.
Which is better? Natural rubber or synthetic rubber?
Natural and synthetic rubbers each have strengths. Natural rubber is great for flexibility, while synthetic rubbers can be customized for specific needs like heat resistance. The best choice depends on the specific application.
How do I select a vibration isolator for my application?
To select the right vibration isolator, start by determining the frequency and amplitude of the vibrations, the weight of the equipment, and the desired level of isolation. Contact the team at RPM for assistance.
What is rubber-to-metal bonding?
Rubber-to-metal bonding involves creating a strong and durable connection between rubber and a metal surface, resulting in a composite material that combines the flexibility and shock absorption of rubber with the strength and rigidity of metal.
What is an engine mount and how does it work?
An engine mount is a flexible component that isolates the engine from the vehicle’s frame, reducing vibrations and noise while allowing for slight engine movement during operation.
What is a rubber sandwich mount?
A rubber sandwich mount is a vibration isolation device consisting of two metal plates with a layer of rubber sandwiched between them, used to reduce the transmission of vibrations.
Ready to get started?
Let Us Be a Small Part of a Big Solution: Your Partner in Building Life Changing Products.
Or Call Us: 888-842-5668