The same qualities that make rubber a desirable material — its flexibility, elasticity, and malleability — also make rubber more challenging to mold than other materials. As a result, design engineers need to consider a number of factors when calculating dimensions.
In order to create a custom rubber part, a manufacturer must determine the critical and non-critical dimensions of the part in order to figure out the best mold design. It may sound basic, but establishing these crucial parameters is more complex than most people realize. This is especially true when designing a high-precision mold.
If you’re unclear on the difference between fixed and closed dimensions and how they relate to tolerances, don’t worry — this article will clear things up. Keep reading to learn about fixed vs. closed dimensions and why they matter.
Rubber Mold Dimensions
A compression mold is essentially two big blocks of steel. To make a mold, manufacturers machine out the custom part’s dimensions on the inside of both steel blocks. When the sculpted blocks squeeze down on a chunk of rubber, they create a molded rubber part. It’s important to understand the functionality of the part so that the appropriate mold design can be made.
Fixed Dimension
The fixed dimension is everything that is machined inside of the steel cavities, the hollow spaces that the rubber fills during the molding process. When the steel blocks compress the raw material, they push the rubber into every part of the cavity, giving it shape.
The biggest consideration when calculating fixed dimensions is making sure that the closed dimensions (the mold dimensions outside of cavities) will fall on an area of the rubber part that is non-critical. The thin line created by the two mold halves coming together is called the parting line, and it’s important to make sure that its placement doesn’t affect part functionality.
Closed Dimension
The closed dimension (also called closure dimension) is anything that is affected by where the two mold halves come together. When the two steel molding blocks squeeze together, they create tremendous pressure on the rubber, causing a thin layer of rubber to eek out between the halves. This excess is called flash, and it can be removed through tumbling or a manual trim.
Several factors affect closed dimensions, including shrinkage, mold maker’s tolerance, trim and finish, flow characteristics of the raw stock, the shape of the preform, and molding process.
In general, flash thickness plays a more prevalent role when creating a small part than a large part. Manufacturers try to design tools and molds that will create as little flash as possible, but it varies by part. Achieving accurate mold dimensions relies heavily on tolerances.
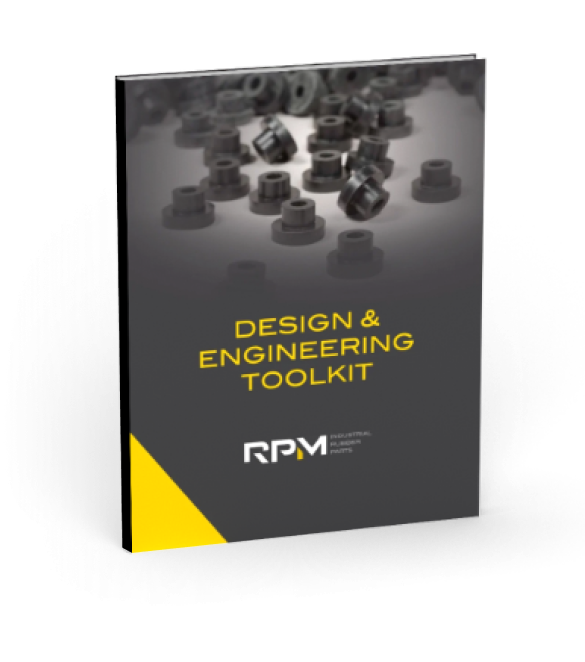
Do you really know everything about designing with rubber parts?
Get a free and valuable resource for finding or custom designing the exact part you need.
Rubber Part Tolerances
Rubber part tolerances, which are also called dimensional tolerances, refer to allowable size variations for rubber products. Establishing these tolerances allows engineers to create products that meet their design requirements.
As tolerances play a critical role in preventing part and process failures, manufacturers should adhere to tolerance tables outlined by the U.S. Tires Manufacturers Association (formerly known as the Rubber Manufacturers Association). These tables outline four levels of engineering tolerances for molded rubber parts:
- A1 – High Precision. This is the tightest tolerance classification and is intended for high-precision rubber products. To achieve A1 precision generally requires expensive molds, fewer cavities, and more in-process controls and inspections than other levels.
- A2 – Precision. This tolerance level indicates precision products and requires that molds be machined and kept in good repair. Although A2 tolerances require a less stringent process than A1 tolerances, they still require careful inspection.
- A3 – Commercial. This tolerance is the standard in the industrial rubber industry. It achieves a quality, economical product, generally through compression molding.
- A4 – Basic. The A4 tolerance is reserved for when dimensional control over a product is secondary to cost.
When choosing a tolerance, designers may instinctively go for the highest level of precision. However, A1 and A2 tolerances are not ideal for all rubber parts, or for all budgets.
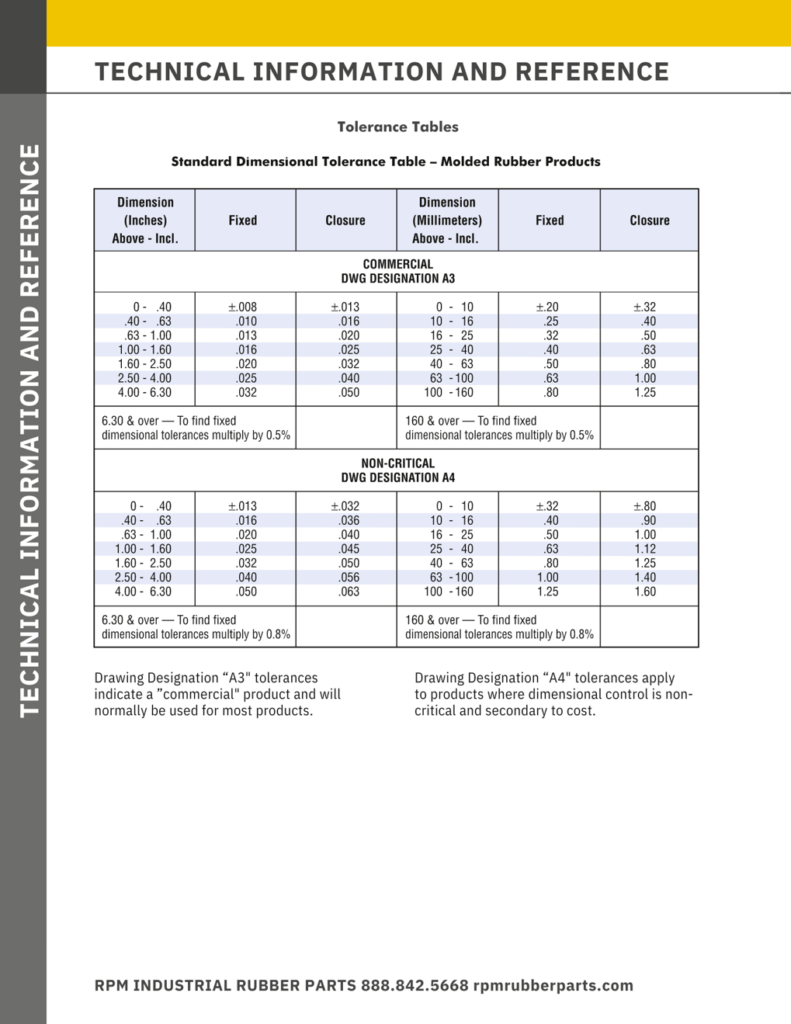
Which Tolerance is Best?
Many people would assume that A1 is the best tolerance, but A1 is only the most precise. The ideal tolerance for your rubber part depends on both the precision needed to achieve functionality and your budget. A1 tolerances require a larger upfront cost and more expensive molds, processes, and controls than other tolerances. If your part functions just as well at an A3, there’s no reason to pay for an A1.
A tiny, complex rubber part might require an A1 or A2 level of precision to achieve its full functionality, and in these cases, we’re happy to manufacture according to high-precision tolerances. However, if tight tolerances are not specified, we generally quote to A3 because it is the most common, standard, and economical tolerance for industrial rubber parts.
Not sure which tolerance your rubber part requires? Consider the size and complexity of your part, as well as its intended purpose. The engineers at RPM Industrial Rubber Parts are happy to help you determine your part’s ideal tolerance.
Applying Dimensional Tolerances
Just like determining tolerance, applying that tolerance requires several considerations. Engineers should keep the following rules in mind:
- Fixed dimension tolerances should be calculated individually, for each fixed dimension, according to size.
- A part’s closed dimension tolerance is determined by the largest closed dimension. This single tolerance is used for all other closed dimensions.
- Fixed and closed dimensions for a particular table don’t necessarily correspond; they can be split between tables.
Additionally, engineers should be careful when applying standard tolerances to products with wide sectional variations. When tolerance is in question, it’s best to consult with the rubber manufacturer.
Industrial Rubber Manufacturing
At RPM Industrial Rubber Parts, we know the key to creating an ideal product is open communication between manufacturer and client. Discussing a rubber part’s intended use, necessary chemical qualities, and application environment — as well as budget and timeline — will help the process run smoothly.
Do you have a custom rubber part in mind? We’d love to discuss your project. Contact us online or give us a call at (888) 842-5668 for more information.
Related Resource
The Engineer’s 7-minute Guide to Rubber Molded Parts
Our free resource is a quick-reference guide to help you determine if exploring a rubber part is right for your application.