Ordering a custom-molded rubber part is an excellent way to get exactly what you are looking for in a product. There are two ways that you can obtain custom molded rubber parts: prototyping and reverse engineering. Each has specific purposes and benefits for custom part manufacturing. Continue reading to learn all about prototyping, reverse engineering, and custom molded rubber services.
Rubber Prototyping
After consultation and design planning, the first piece a customer will often receive from a manufacturer will be the prototype. A prototype is a model of the part that was requested. The prototype model is usually 3D printed or molded. A prototype may undergo multiple iterations until the exact design and specs are achieved. Once the customer is satisfied, the prototype will be used to create rubber molds for volume production.
Why Should I Choose Prototyping?
There are a few situations in which you may want to choose prototyping over reverse engineering for a custom-molded rubber product:
- You want to test the elastomer in operating conditions – such as fluid exposure, heat exposure, etc.
- The part that you are requesting is entirely unique to your product
- You require specific dimensions or a design that may not be offered as a standard part
- You want to test the part before you request a full volume
- The part that you need requires a specific material, like EPDM or silicone
If any of the above applies to the custom rubber part you are looking for, then you may want to choose prototyping instead of reverse engineering.
Rubber Compression Molding for Custom Rubber Prototypes
If a customer is looking for a molded prototype rather than a 3D printed one, then the best method is compression molding. This rubber molding process takes place through a few steps:
- The elastomer material is placed into the mold
- The elastomer is compressed and cured at high pressure and temperature
- The rubber part is removed from the mold
This is the best method for custom rubber prototypes because compression molding is ideal for low-volume production and individual parts.
It is often very economical in the long run – at RPM we can create a single cavity mold that will allow us to produce the mold and part in a fairly quick timeline.
The advantage of going the prototype mold route vs 3D printing is that you are able to test the proper elastomer in the application to make sure there are no surprises as your part enters production. 3D printed items while good for fit & form – lack the available materials to be printed with. You are often not able to test the proper elastomer in the application – CAD modeling can only take you so far.
Reverse Engineering
What do you do when you have an existing part but no drawings, specs, or even a place to purchase? Scrap your machine because that rubber component is no longer available? When it comes to custom rubber products, sometimes the part that a customer requests is not entirely unique. At RPM, our team often receives requests to mold that matches an existing part or is similar to a part already in use. This approach for custom molded products would call for reverse engineering. Using a current piece to create a new piece is a great way to save money and time, and often the right option for OEMs that want an easy custom part process or just to replicate a function that is known to work.
Why Should I Choose Reverse Engineering?
There are many reasons to choose reverse engineering instead of prototyping. Here are a few:
- A part you use has been discontinued
- You are looking for a higher quality version of a part you use
- You need a part made in a different material or need a slight modification
- The price of a part that you use has changed
If you find yourself needing a replacement for a part that you no longer can or want to use, then reverse engineering would be an excellent option to obtain the right molded parts.
Rubber Injection Molding for Custom Rubber Reverse Engineering
While compression molding is typically more economical, it isn’t always the best method. If your part needs tight tolerances or has unique features. The best method for custom rubber reverse engineering is injection molding. This is because, with injection molding, rubber manufacturers can easily create molds for volume production while maintaining tighter tolerances due to the mold construction.
There are a few steps to injection molding:
- The elastomer is fed into the system and turned to a pliable flow state.
- The injector pushes the flowable elastomer into the mold
- The mold is cured at high pressure and temperature
- The part is removed from the mold
When customers request reverse engineering, they typically want high volume production, which makes injection molding a good choice.
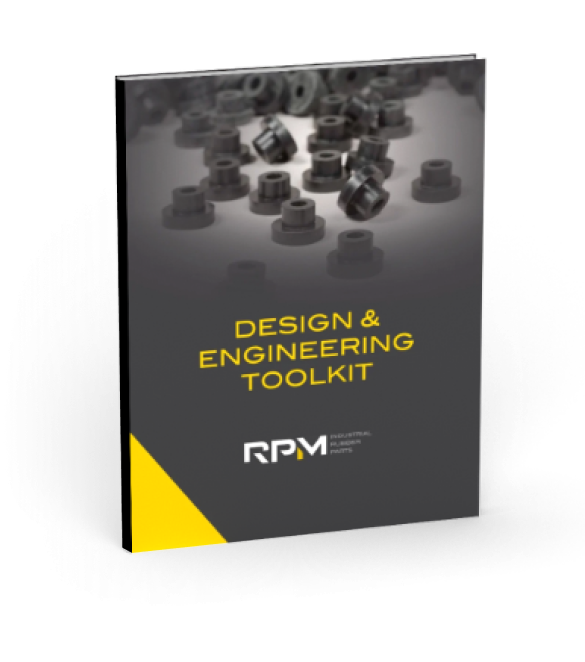
Do you really know everything about designing with rubber parts?
Get a free and valuable resource for finding or custom designing the exact part you need.
Custom Molded Rubber Prototyping and Reverse Engineering Services
If you are looking for an excellent custom molded rubber service, RPM Industrial Rubber Parts can help. RPM serves a variety of industries: automobile, medical, defense, construction, and more. Each molded rubber component is designed by engineers and manufactured by experts. After decades of experience, we understand the right tooling, rubber compound options, metal bonding processes, and more that will achieve reliable, useful custom rubber products. Our team provides both high-quality prototyping and reverse engineering services.
RPM Custom Molded Rubber Process
There are three steps to our custom molded rubber process that ensure our clients get the exact parts they need.
- Design Your Custom Rubber Component: When you request a custom part from RPM, you will work with one of our in-house engineers to design the part you want. If you already have design plans, we can use those to help create your custom part. However, no need to worry if you don’t have design plans for the part that you need. Our team is happy to assist you in creating a plan with the dimensions and design of the part that you require.
- Model is Sent Until Satisfied: Once your design has been completed, our engineers will use it to create a mold of the part. Whether you have chosen prototyping or reverse engineering, you will receive a model of the part that you want. The model is created using a molding method, most likely compression molding. Our team will continue to refine the part until you are satisfied with it. We do this to make sure that the part is exactly what you are looking for.
- Product is Shipped: When you are satisfied with the model that we send you, we will ask you to choose the elastomer material that you want for the part. Then, we will produce the part at full production volume. We typically use injection molding for high-volume parts due to the speed at which it creates parts. Once the part has been produced, we will ship it to you and you can begin using it in your products.
For the highest quality custom molded rubber products designed by professional engineers, choose RPM Industrial Rubber Parts. To find out about our custom rubber parts and standard parts, contact us at (888) 842-5668.
Related Resource
The Engineer’s 7-minute Guide to Rubber Molded Parts
Our free resource is a quick-reference guide to help you determine if exploring a rubber part is right for your application.